What's new in injection moulding?
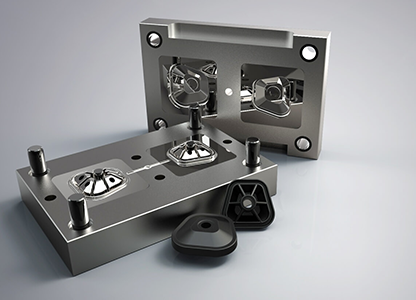
Injection moulding innovations: pushing the boundaries
In the manufacturing toolbox, injection moulding stands out as a vital process for creating a wide range of products, from simple everyday items to intricate components used in advanced technologies. Over the years, advancements in injection moulding techniques have revolutionized the way products are designed and manufactured en masse. In this article, we will delve into the latest innovations in injection moulding, focusing on complex mould design and the use of advanced materials, and how these innovations are pushing the boundaries to enable the creation of more intricate and durable products.
Complex mould design: redefining possibilities
One of the key innovations in injection moulding is the development of complex mould design capabilities. Traditional moulding techniques were limited in terms of the shapes and intricacies that could be achieved. However, with the advent of advanced software and technologies such as computer-aided design (CAD) and computer-aided manufacturing (CAM), manufacturers can now create moulds with intricate geometries and complex features that were once deemed impossible.
Complex mould designs allow for the production of highly detailed and customized products that cater to specific industry needs. Read the article about induction heat/cool technology. Whether it's creating intricate patterns on the surface of a product or designing components with precise tolerances or (composite) inserts, complex mould design has opened up a world of possibilities for manufacturers looking to differentiate their products in the market.
Advanced materials: enhancing performance and durability
In addition to complex mould design, the use of performance materials has been another game-changer in the field of injection moulding. The traditional materials used in injection moulding, such as various types of polyolifins, have now been supplemented with a wide range of advanced adidtives, like long fibres, natural fibres, and laser markable pigments that offer superior performance and durability.
Materials like PEEK, PEI, and elastomers (TPU's) are now commonly used in injection moulding to meet the demanding requirements of modern applications. These materials exhibit properties such as high strength, heat resistance, chemical resistance, and flexibility, making them ideal for a diverse range of industries, including aerospace, automotive, electronics, and healthcare.
By leveraging advanced materials in conjunction with complex mould designs, manufacturers can produce products that are not only visually appealing but also highly functional and long-lasting. From intricate medical devices to durable automotive components, the possibilities are endless when it comes to creating innovative products through injection moulding.
Pushing the boundaries: the future of injection moulding
As injection moulding continues to evolve, it is clear that the future holds even more exciting possibilities. Innovations in areas such as additive manufacturing, nanotechnology, and Industry 4.0 are poised to further revolutionize the way products are designed and manufactured combined with injection moulding techniques, think laser marking special compounds for new functionality for one.
With a focus on sustainability and efficiency, manufacturers are exploring new ways to minimize material wastage, reduce energy consumption, and optimize production processes. Additive manufacturing techniques like 3D printing are also being integrated into injection moulding workflows, enabling rapid prototyping and customized production at a fraction of the time and cost.
In conclusion, the advancements in complex mould design and the use of advanced materials have propelled injection molding to new heights, enabling manufacturers to push the boundaries of what is possible in product design and manufacturing. As we look ahead to the future, the continued innovation and integration of cutting-edge technologies will undoubtedly unlock even greater potential for creating intricate, durable, and groundbreaking products through injection molding.

Discover related Insights
Stay up to date with our latest articles.