Plastic rotation moulding big parts
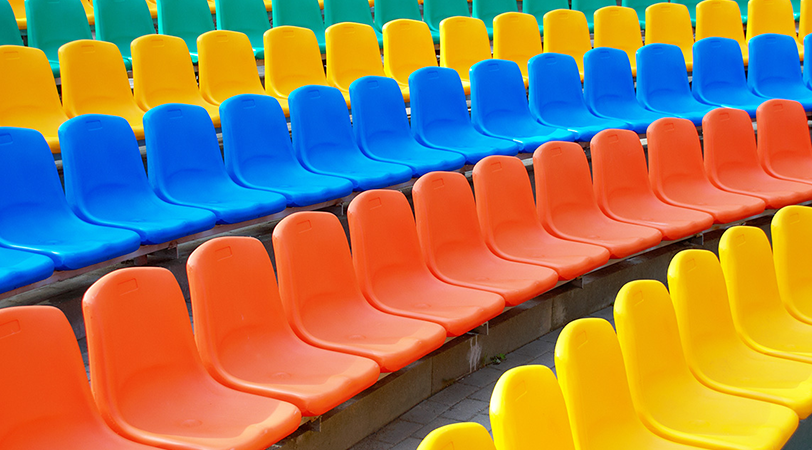
Rotational moulding: large plastic manufacturing
In manufacturing, innovation plays a vital role in shaping the way products are created. One such revolutionary process making waves in the industry is rotational molding. This technique has transformed the production of large, hollow plastic items, offering a myriad of benefits that have propelled its popularity in the manufacturing sector.
Unique ability to produce large, hollow plastic items
Rotational moulding, also known as rotomoulding, is a manufacturing process that involves heating and rotating a hollow mould filled with a powdered polymer material. The mould rotates on two axes simultaneously, ensuring the even distribution of the material, resulting in products with uniform thickness. This unique method allows for the creation of large, complex, and hollow plastic items that would be challenging or impossible to produce using traditional manufacturing techniques.
New innovations in the industry are altered heating systems and better sensor grids for even heat distribution to alter process control parameters. From better surface quality and detailling, to more control over surface thickness and cycle times.
Benefits of rotational moulding
1. Uniform thickness: One of the key advantages of rotational molding is the ability to create products with consistent wall thickness. This uniformity enhances the structural integrity of the final product, making it durable and reliable.
2. Low-cost tooling: Compared to other moulding processes, rotational moulding requires relatively inexpensive tooling. Since moulds are not subjected to high pressures or temperatures, they can be made from cost-effective materials such as aluminum or even fabricated composites, reducing production costs significantly.
3. Design flexibility: Rotational moulding offers unparalleled design flexibility, allowing manufacturers to create products with intricate shapes, undercuts, and complex geometries. This adaptability enables companies to bring innovative and customized products to market quickly and efficiently.
Applications in various industries
Rotational molding has found extensive applications across a wide range of industries, including the production of storage tanks, small boats, automotive parts, playground equipment, and even medical devices. The versatility of this manufacturing process makes it an attractive choice for companies seeking to manufacture large plastic items with intricate designs.
In conclusion, rotational moulding has revolutionized the way large plastic items are manufactured, offering a cost-effective, versatile, and efficient production method. With its ability to produce products with uniform thickness, low-cost tooling, and design flexibility, this innovative process continues to grow in popularity, driving advancements in various industries. Embracing rotational moulding opens up a world of possibilities for manufacturers looking to push the boundaries of design and production in the dynamic landscape of plastic manufacturing.
Innovation and adaptability are key in the competitive world of manufacturing, and rotational moulding stands out as a game-changer in shaping the future of large plastic manufacturing.

Discover related Insights
Stay up to date with our latest articles.