How is plastic extrusion adding to the product landscape
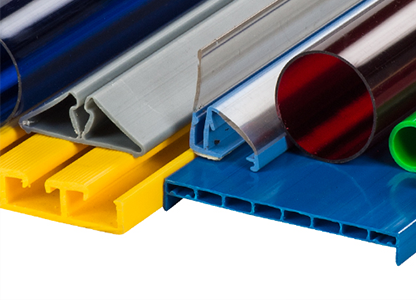
Plastic extrusion: transforming products with versatility
In the field of manufacturing, few processes have revolutionized the industry quite like plastic extrusion. Plastic extrusion is a method used to create objects of a fixed cross-sectional profile. It involves melting raw plastic material and shaping it into a continuous profile by pushing it through a die (extrusion). This process has transformed manufacturing by offering cost-effective solutions and remarkable versatility in producing a wide array of products ranging from piping to window frames.
The plastic extrusion process
The plastic extrusion process is both simple and efficient. It typically involves the following steps:
- Material Feeding: Plastic resin pellets or powder are fed into the extruder, where they are gradually heated and compressed.
- Melting: The heat and pressure inside the extruder (barrel) melt the plastic pellets, turning them into a viscous liquid.
- Shaping: The molten plastic is then pushed through a die, which imparts the desired shape to the material.
- Cooling and Cutting: Once the plastic has taken the shape of the die, it is cooled using air or water and then cut to the desired length.
Cost-effectiveness of plastic extrusion
One of the most significant advantages of plastic extrusion is its cost-effectiveness. The process allows for high-volume production at a relatively low cost per unit. Since extrusion can be continuous, it enables manufacturers to produce large quantities of uniform products in a shorter amount of time compared to traditional manufacturing methods. This efficiency ultimately translates to cost savings for both manufacturers and consumers.
Versatility in product range
Plastic extrusion offers unparalleled versatility in the range of products that can be manufactured. From simple tubes and pipes to complex window frames and profiles, plastic extrusion can create products of varying sizes, shapes, and complexities. A special group of plastic extrusion is packaging film and extrusion blow moulding, for garbage bags etc. It is widely utilized in industries such as construction, automotive, and packaging, showcasing its adaptability to meet diverse manufacturing needs.
Advancements in extrusion technology
With technological advancements, plastic extrusion has evolved to offer even more capabilities. Co-extrusion, for example, allows for multiple layers of materials to be extruded simultaneously, creating products with enhanced properties such as increased strength or barrier protection. Co-extrusion combined with braiding to make a fluid preassure hose, or a special tooling to make harnass hoses. Additionally, the use of recycled materials in extrusion processes has gained traction, contributing to sustainability efforts and reducing environmental impact.
Conclusion
In conclusion, plastic extrusion has undoubtedly transformed manufacturing with its cost-effectiveness and versatility. From its streamlined process to the wide range of products it can create, plastic extrusion continues to be a cornerstone of modern manufacturing. As technology advances further and sustainability becomes increasingly important, the future of plastic extrusion seems poised to soar to new heights, offering endless possibilities for innovation and development in the manufacturing industry.

Discover related Insights
Stay up to date with our latest articles.